TYPES OF CERAMIC BEARINGS
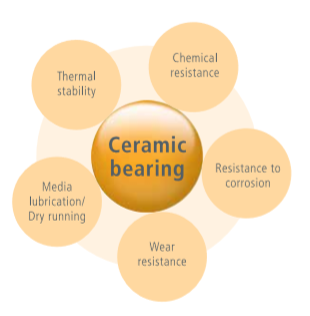
Technical ceramics are the latest materials used for rolling bearings and show excellent performance
Ceramic materials are environmentally compatible, stable at high temperatures, insulating and exceptionally durable. In comparison to steel, ceramics are much harder, have a lower density and are more resistant to wear and corrosion. The combination of the advantageous properties make ceramic bearings very well suited for extreme mechanical, chemical, and thermal stress conditions, as occur for example, in the chemical industry, thermal engineering (e.g. furnaces), pumps, roller mills, galvanizing units or steam boilers.
Due to materials characteristics, ceramic rolling bearings are well-suited for applications with media lubrication and even dry running conditions. These bearings therefore find use in any area where hygiene is of crucial performance:
- Food industry
- Pharmaceutical industry
- Clean room technology
- Medical science
- Vacuum technology
Materials Properties | Si3N4 | ZrO2 | AI203 | 100Cr6 | ||
---|---|---|---|---|---|---|
Density | ρ | g/cm³ | 3,2 | 5,9 – 6, 04 | > 3,9 | 7,85 |
Vickers Hardness | HV10 | N/mm² | > 1700 | 1300 | 1800 | 700 |
Young’s Modulus | E | GPa | 300 | 205 | 390 | 210 |
Coefficient of Thermal Expansion | α | 10-6/K | 3,2 | 10,2 | 8,2 | 11,5 |
Bending Strength | δB | N/mm² | > 800 | 1000 – 1500 | 380 | >2500 |
Fracture Toughness | KIC | MPa m½ | 8 | 8 – 12 | 4 – 7 | >20 |
Thermal Conductivity | λ | W/m * K | 30 – 35 | 2 | 27 | 40 – 45 |
Spec. electric resistance | ρ | Ωm | 1012 | 109 | 1012 | 10-7 – 10-6 |
Grain size | d | µm | < 1 | < 1 | 1 – 5* | – |
Different qualities are available on request, depending on the area of application.
Materials properties of silicon nitride, zirconium oxide, aluminium oxide and bearing steel.
In comparison to steel, technical ceramics are up to 60% lighter. have a 70% lower thermal expansion coefficient and are up to three times as hard. The high values for hardness and Young’s modulus provide a 70% increase in stiffness and up to a 40% decrease in the coefficient of friction. Unlike steel, ceramic materials exhibit very low adhesive wear, due to the different chemical bonding characteristics. New developments in the field of nano-materials have led to considerable improvements in the critical properties of ceramics as e.g. fracture strength and fracture toughness.
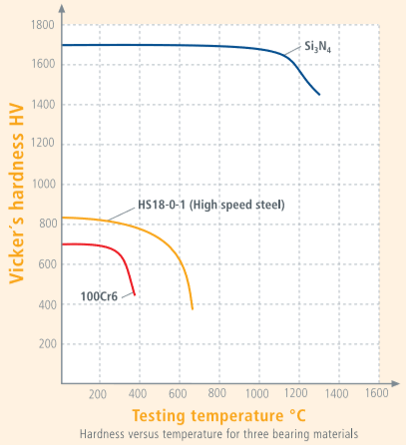
Si3N4
is the preferred material for ceramic bearings due to its specific tribological characteristics. It is a lightweight, strong and thermally stable material with a low thermal expansion coefficient, making it well suited for applications in temperatures of up to 1000 °C or in conditions with strong fluctuations in temperature. The low weight leads to low centrifugal forces under high-speed conditions, and this result in reduced friction and wear and longer lifetime.
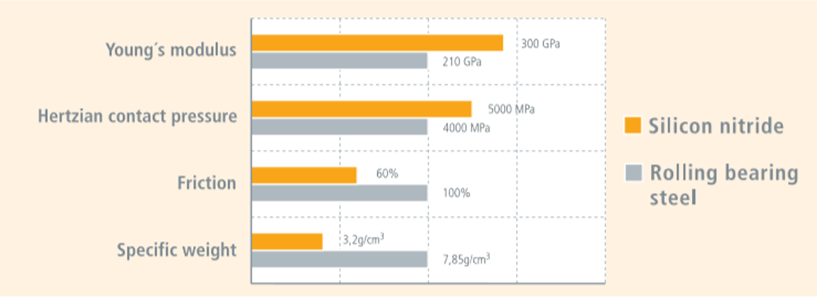
Comparison of the chemical properties of steel and silicon nitride. These properties are crucial for the tribological behavior of bearing materials and are what makes silicon nitride the first choice material for high-performance rolling bearings.
Silicon nitride displays excellent corrosion resistance, particularly in very strong acids and Iyes. A low-cost alternative to silicon nitride is zirconium oxide. This material has lower chemical stability and thermal stability properties. One big advantage of zirconium oxide, however, is that its coeffecient of thermal expansion is similar to that of steel, thus very few problems arise with regard to component assembly, e.g. when mounting the bearing on metal shaft.
Chemical stability | Si3N4 | ZrO2 | AI203 | 100Cr6 | X105CrMo17 (AISI 440c) |
---|---|---|---|---|---|
Hydrochloric acid HCI (diluted) | + | + | + | – | – |
Hydrochloric acid HCI (concentrated) | + | (+) | + | – | – |
Nitric acid HN03 (diluted) | + | + | + | – | + |
Nitric acid HN03 (concentrated) | + | (+) | + | – | + |
Sulphuric acid H2S04 (diluted) | + | + | + | – | – |
Sulphuric acid H2S04 (concentrated) | + | (+) | + | – | – |
Phosphoric acid H3P04 | + | + | + | – | – |
Hydroflouric acid HF | – | – | – | – | – |
Sodium hydroxide Na0H solution | + | + | + | – | + |
Potassium hydroxide K0H solution | + | + | + | – | + |
Sodium chloride NacCl | + | + | + | – | – |
Potassium chloride KCl | + | + | + | – | – |
Copper chloride CuCI2 | + | + | + | – | – |
+ Stable | (+) some reaction | – unstable
The bearings from Sintertechnik GmbH have insulated characteristics and don’t interact with magnetic fields. Thats why these bearings work well in situations when, for example, steel bearings might interfere with magnetic fields (e.g. nuclear spin tomography), or when electric arcs might form and cause damage of bearings. Whenever a voltage is applied to a steel bearing an electric current is induced. This current will cause damage due to crater formation, on-top plating or the formation of riflles both on rolling parts and on the track, and such a case might occur e.g. in electric motors or in machines used to transport paper or plastic films. A further problem by voltage discharges between the outer and the inner ring is premature lubricant ageing.
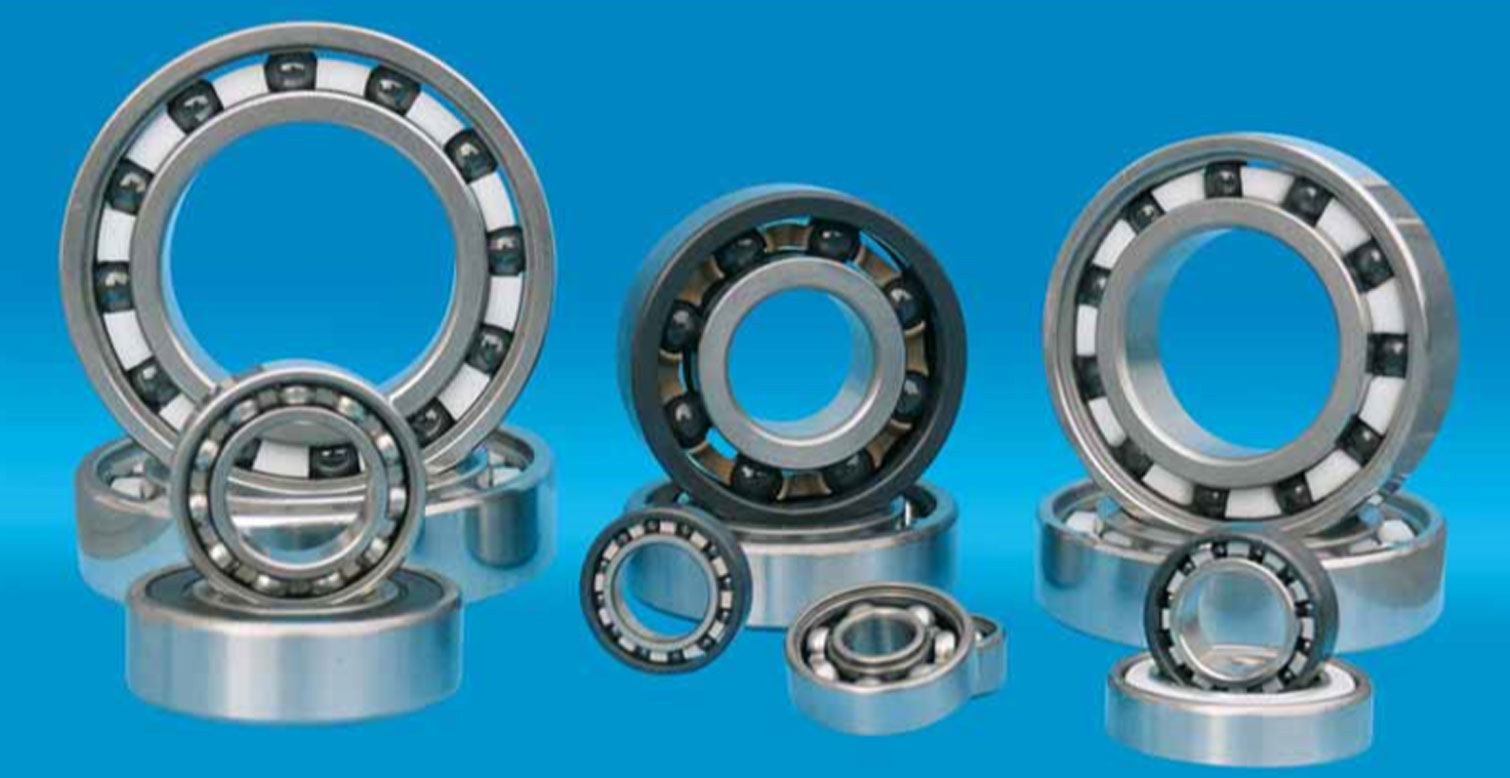
HYBRID BEARINGS
Hybrid rolling bearings are basically a combination of steel rings with ceramic balls. Such hybrid bearings are used as low-cost alternative in applications where steel bearings would not meet given technical requirements. One of the main features of hybrid bearings is the low weight of the sliding elements, a fact that reduces friction as well as the need for lubrication. The result is a bearing that boasts a longer lifetime than standard steel ball bearings. The low affinity between ceramic and steel also reduces adhesive wear, which would lead to cold welding spots between track and ball. A further advantage is the high Young’s modulus, which provides a small pressure ellipse.
Sintertechnik GmbH ceramic balls for hybrid bearings are available in silicon nitride or zirconium oxide are manufactured to precision class G10 (deviation of ball diameter < 0,25 µm, deviation of sphere < 0,25 µm and deviation of the surface roughness Ra < 0,025 µm).
Hybrid bearings have lower friction and develop far less heat during running than steel bearings. As the upper speed limit of bearing depends mainly on heat development, speed might be raised – depending on running conditions – by up to 30% of that possible with steel ball bearings. Hybrid bearings may therefore improve machinery and system performance.
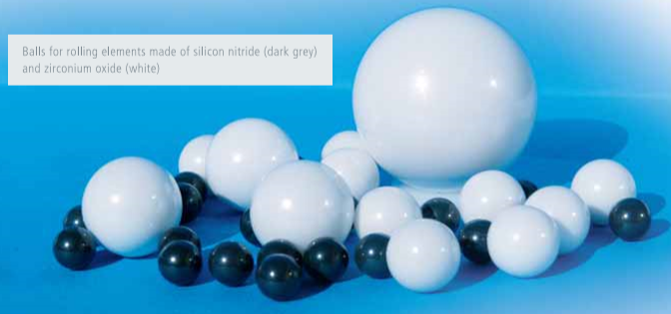
The picture below shows temperature development in dependence of speed of rotation, for a bearing containing either steel balls or ceramic balls.
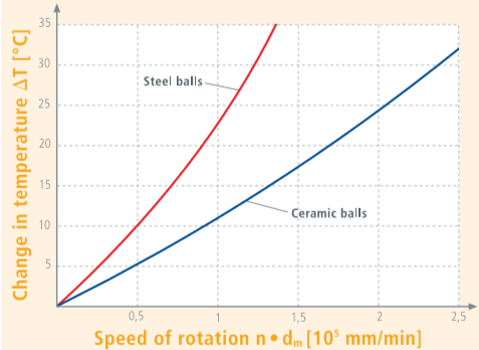
Steel | Hybrid | Ceramic | |
---|---|---|---|
Chemical stability | – | 0 | + |
Thermal stability | – | – | + |
Media lubrication | – | 0 | + |
Magnetic interaction | – | – | + |
Electric insulation | – | + | + |
Dry running conditions | – | 0 | + |
Stiffness | – | – | + |
Weight | + | 0 | – |
Price | + | 0 | – | Effective Costs | – | 0 | + |
THIS IS SINTERTECHNIK
Sintertechnik GmbH is a German company founded in 1962, specialized in the development and production of high tech material components. Sintertechnik has been established as an important research partner for well-known industrial companies and aviation and space technology companies. Our clients are i.e. the global leaders in propusion technology – for more than 35 years. Materials produced and processes developed by Sintertechnik GmbH have proven their reliability in aerospace applications or on the planet Mars and are used for i.e. zero-g parabolic flights. We are glad to receive any new request for your customer specific material solution!